By Rebecca Knolle, P.E., PMP, LEED AP, M.SAME
After analysis showed the cost-effectiveness of preserving the original 1940s-era windows for Hangar One at Wright-Patterson AFB, a careful renovation followed that restored its functionality while conserving important history.
The Airplane Repair Dock at Wright-Patterson AFB, Ohio, known as “Hangar One,” was designed some 80 years ago by the famed industrial architect Albert Kahn, a pioneer in industrial building design. The six-story hangar has receiving bays that are large enough to accommodate two Boeing 747 aircraft. Kahn also incorporated windows in its design to bring in natural lighting as well as ventilation in a period when air conditioning was not widely available. The east and west side concrete walls of the structure feature a total of 12,000 steel-framed window panels.
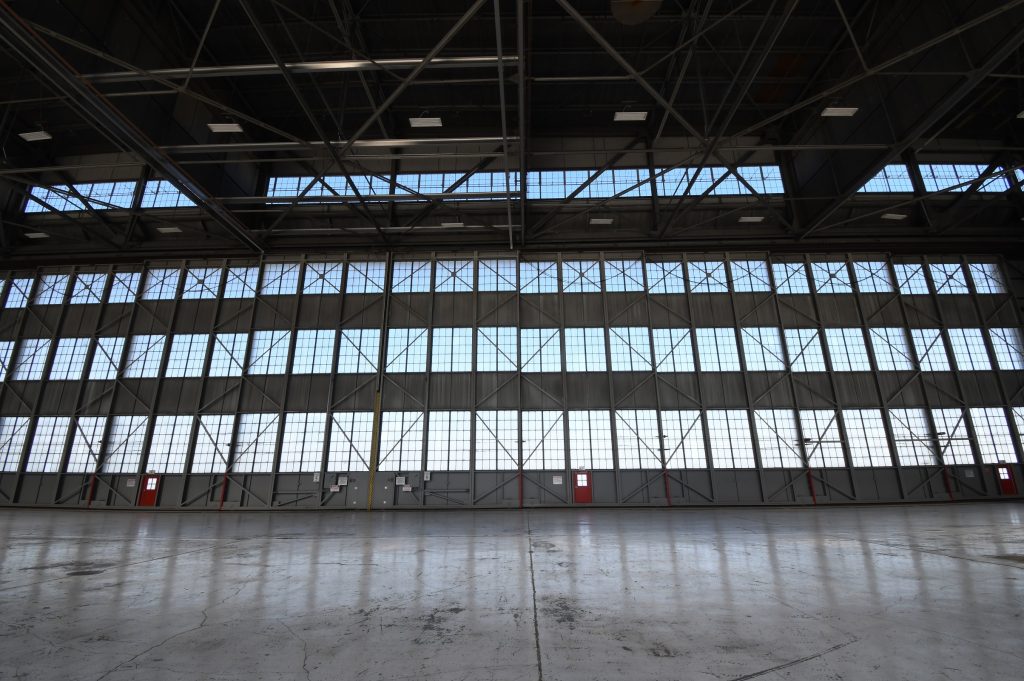
PHOTOS COURTESY OF WOOLPERT
After nine decades of enduring western Ohio weather, however, it was time for a comprehensive restoration effort in order to maintain readiness while preserving the historic hangar.
Those overseeing planning for the renovation project had a choice: remove all the windows and steel frames and replace them with new, aluminum-sash ones; or restore and preserve the existing window panels and frames. In either case, the original windows and steel frames would need to be cleaned of asbestos and lead paint before they could be reused or discarded and recycled. But while the first option may have been more cost-effective, it would lose some of the appeal that makes storied installations like Wright-Patterson so unique.
Historic building restorations typically call for replacing old, outdated windows with new, more secure, thermally efficient windows. Preserving and reusing original construction materials is often cost-prohibitive. Replacement windows also improve insulative qualities. On this project, a rare blend of circumstances led to preserving and restoring many of the iconic windows. Moreover, the quality of design and construction from a past decade in many ways is unmatched even with today’s technological advances and knowledge base. Being able to maintain history in built form is important and rewarding because the work is preserving both the original design and the building’s stories.
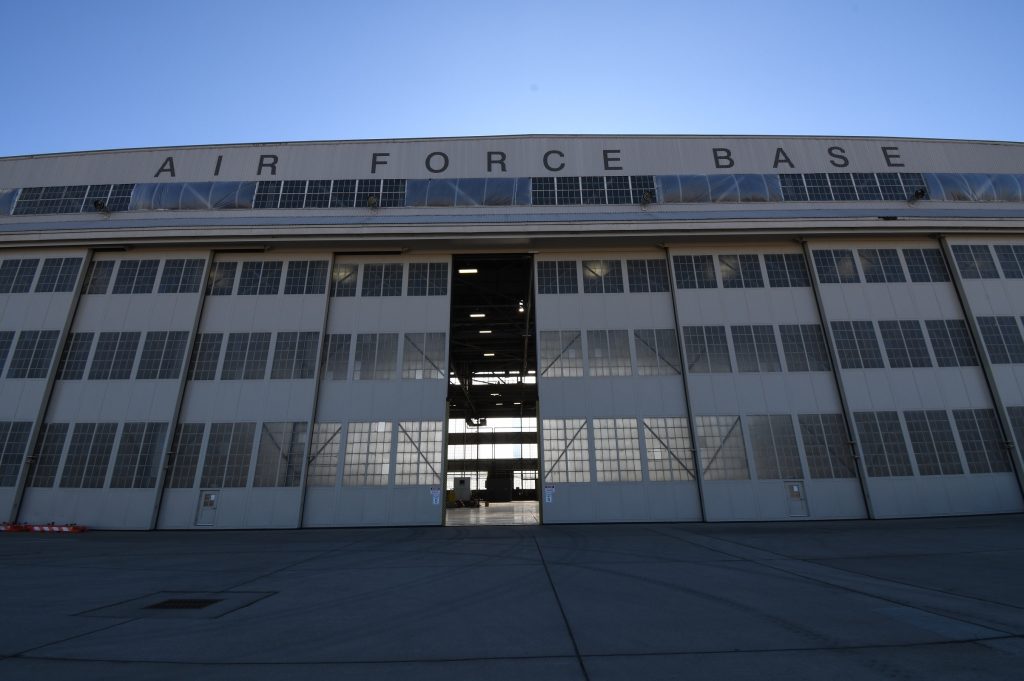
Determining Direction
Hangar One has served many purposes over the years. Currently, it houses the largest aircraft that visit Wright-Patterson, including Air Force One. The hangar is frequently used to repair and maintain aircraft. In addition, it houses personnel in office space that was built between the facility and the adjacent hangar.
Woolpert was hired to plan the renovation work of the facility, which began with a lifecycle cost analysis. This mandatory step in government contracts involved an environmental assessment and consulting with contractors that specialize in window restoration.
Environmental Assessment. The cost analysis, which presented a package of options and made a recommendation on the most cost-effective route, was pivotal in determining which direction to take. For Hangar One, the cost analysis included a number of factors. Chief among these is that the hangar is listed on the National Register of Historic Places; any plans to restore it had to be approved by the State Historic Preservation Office. To conduct the environmental assessment, a subcontractor was brought in to test all the materials. It was then found that there was a lot of asbestos in the caulking around the windowpanes and the frames were coated with lead paint. The environmental assessment helped determine what it might cost to remediate the hazardous materials.
Windows in occupied structures on military bases need to be blast-proof in case of an explosion. Occupied structures also need to meet current standards for insulative properties. However, because the hangar is not considered an occupied structure, that provided the leeway to consider restoring and reusing the existing windows. Heating and cooling likewise was not an issue, and the cost to remediate was the same whether the windows were replaced or not. In the end, the cost analysis showed it would be more cost-effective to keep the old windows.
Making the Old New
The original windows from 1941 are true divided, light, steel-framed windows. They are constructed in units, ranging in size from 10-ft, 4-in to 5-ft in height and from 2-ft, 5-in to 6-ft, 10-in in width.
The hangar has been renovated and expanded over the years. This included the addition of a new air control tower in 2003. The windows on every wall have been impacted during these construction periods. Replacement windows, with the glass and framing fabricated to replicate the original design, were installed in 2014 on the east side elevation. There are also clerestory windows that function on a lever and pulley system. When these and the lower-level windows are both open, air circulates throughout the large hangar. The manual operating parts and system for the clerestory windows were restored in addition to the windows to maintain the building’s function for ventilation.
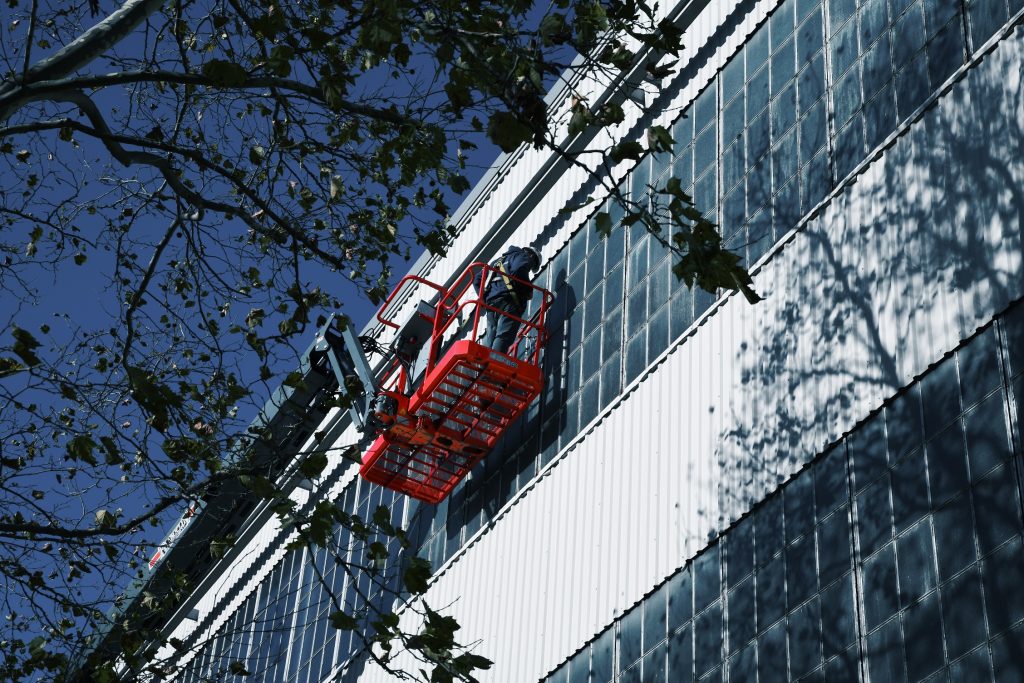
Measured Approach. To conduct the renovation, each window in the facility had to be measured, which required meticulous effort, mentally and physically, by climbing up to the many roof locations and then measuring, documenting, and translating the data to physical drawings. While challenging, this work served an important purpose in helping revitalize the structure while maintaining the operable capabilities of the windows. In addition to the careful work of measuring the windows, the team also needed to implement a detailed plan to accommodate the renovations so that aircraft work could continue in the area of the hangar that was not impacted by the window restoration and replacement. Since the hangar, and the personnel working inside, have to be ready at any given time to respond to emergency calls for service, the structure needed to be kept open and functioning as much as possible.
The windows are made of textured glass, which lets light in but does not allow someone from the outside to see what is inside the building. The levered, clerestory windows are now functional and can be opened to lessen the pressurization and depressurization of the opening and closing of the hangar doors.
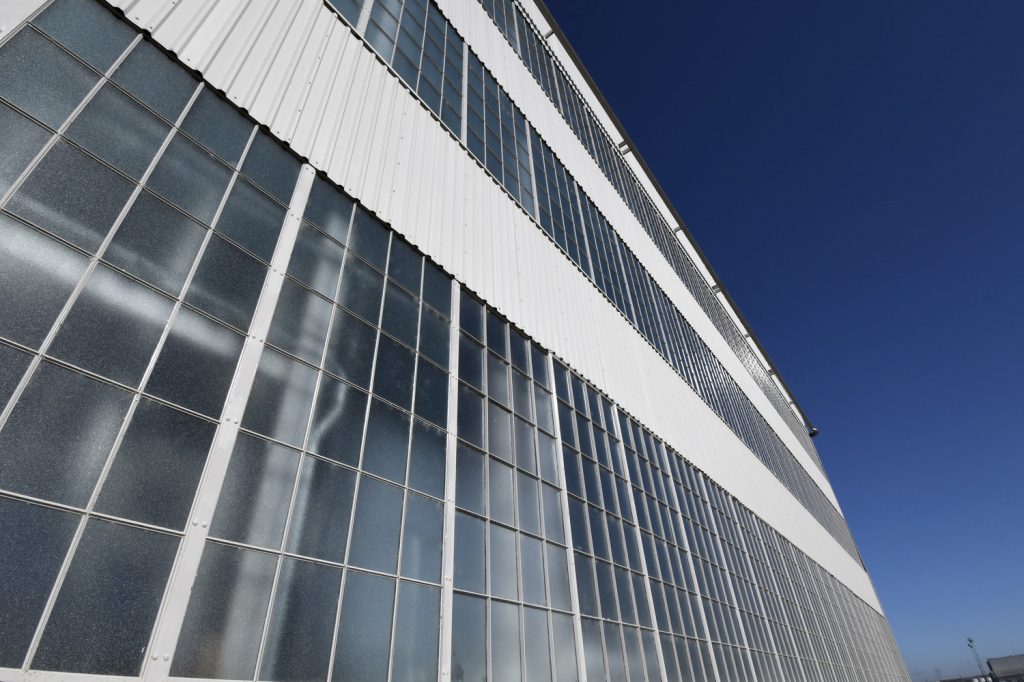
Functional & Classic
Hangar One continues to be just as active and vital to U.S. Air Force operations as it was during the 1940s when first constructed. While the passage of time has changed how the building looks and operates, the functionality it offers is just as relevant today as it was when it was first designed.
With the original windows restored, airmen of the 21st century who work in the historic hangar can enjoy the functionality of the renovation along with the classic industrial aesthetic look that can only be achieved using original materials. In the time since the project was completed a few years ago, it is clear that the blend of old and new can serve an enduring purpose in designing modern structures without losing historical influence.
Rebecca Knolle, P.E., PMP, LEED AP, M.SAME, is Project Manager, Airport and Aviation Design, Woolpert; rebecca. knolle@woolpert.com.
More News from TME
-
Developing an Engineering Standard of Care for Cyber Safety
There is growing urgency to secure the nation’s critical infrastructure from a cyberattack, which will require improvements in both federal policies and day-to-day operations to strengthen response and recovery from incidents. -
Improving Escalation Forecasting in Federal Construction
A newly developed escalation forecasting methodology for major capital acquisition projects improves on previous models with a Monte Carlo simulation to increase accuracy. -
Reducing Health Risks When Working in Confined Spaces
Completing an audit of the hazards, permits, and roles and responsibilities associated with confined spaces can help alleviate health risks and enhance worker protections around these aspects of facilities.