By Zakary Payne, P.E., M.SAME, Tracy Meeks, P.E., M.SAME, and Lt. Col. Josh Aldred, Ph.D., P.E., PMP, M.SAME, USAF
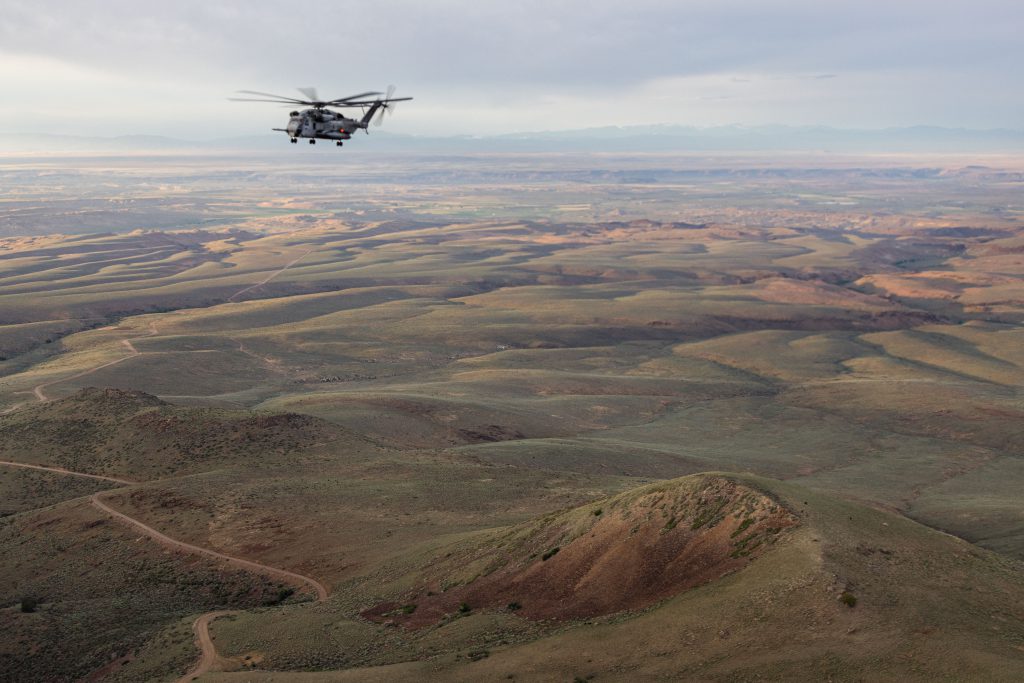
Located roughly 50-mi south of Boise, Idaho, past rolling fields of wheat, barley, and alfalfa, is Mountain Home AFB. While the visually unremarkable installation and its pastoral surroundings might suggest that little unusual is going on here, nothing could be further from the truth.
The home of the 366th Fighter Wing’s Gunfighters is recognized across the Department of the Air Force as a base that enthusiastically pursues opportunities for innovation. In 2018, Mountain Home tested a new wing organizational concept aimed at flattening the decision-making structure to encourage faster, decentralized execution. Similarly, the base was recently selected as the preferred alternative for the Qatar Emiri Air Force’s F-15QA training mission, and Republic of Singapore F-15SGs have been roaring overhead since 2009. Remarkably, the base is likely to soon have the rare distinction of hosting two such unique missions.
Mountain Home is also innovating through aggressive digital transformation. For the last 15 years, the Air Force Civil Engineer community has honed its asset management principles and practices to improve how it provides facility and infrastructure support. A cornerstone of this transformation is improving asset visibility, defined by the Department of Defense as “the ability to provide timely and accurate information on the location, quantity, condition, movement, and status of items in its inventory.”
A significant number of resources were deployed to collect asset information, and additional IT systems were brought online to house these data. While this represented a marked improvement to overall asset visibility, the true benefits have yet to be felt because base-level processes and procedures have not evolved in step with these digital changes. However, Mountain Home’s 366th Civil Engineer Squadron saw an opportunity to remedy this and used systems architecture to re-engineer acquisition workflows, improve space management tools, and create a digital twin prototype using commercial-off-the-shelf products.
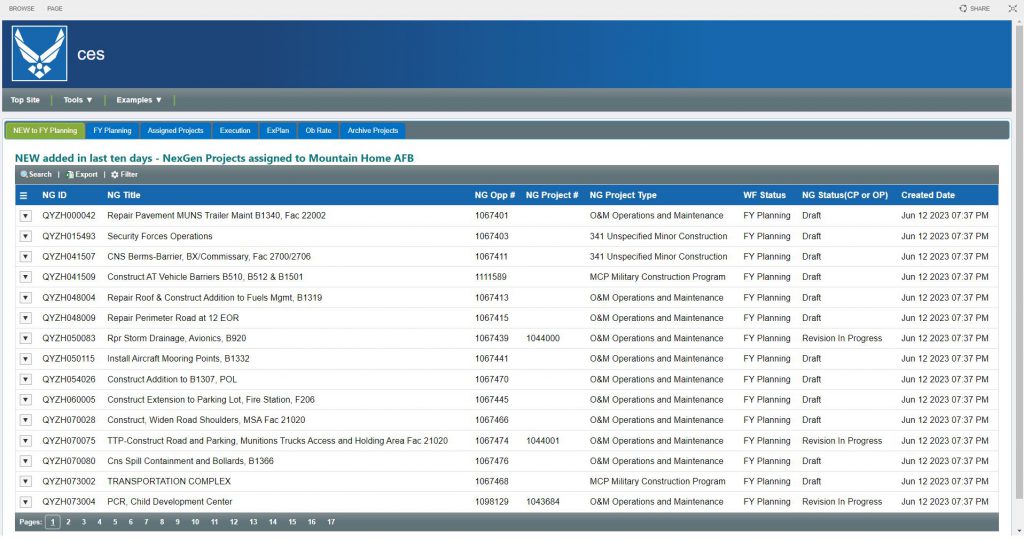
Workflow Modernization
The first foray into digital transformation came as the result of a Rapid Improvement Event facilitated by JJR Solutions and Matrix Design Group. Each step of the engineering flight acquisition process was analyzed—from requirements definition and contract award through design, construction, and closeout. This effort defined the engineering flight’s system architecture by visualizing people, processes, and technology, while identifying key friction points and significant challenges with communication, collaboration, and consistency.
As an example, a thorough review of construction project files over the course of three fiscal years demonstrated that there was no consistency in the acquisition documents and specifications used, despite the fact that standardized contract vehicles were employed.
Similarly, the base engineers lacked an efficient means of tracking the status of acquisition packages and construction projects. Often, information was simply emailed from one organization to another, while other times a file exchange system was used. Both methods lacked the ability to track the current location of an acquisition package in an automated fashion. None of the users could see how long the packages were taking at each step along the way. This made it impossible to maintain a reliable obligation schedule throughout the fiscal year. Up to 10 hours per week were spent manually updating and maintaining a cumbersome project-tracking database, which the airmen described as “always out of date.” Clearly, an automated, digital solution was needed.
Recognizing the Air Force’s familiarity and proficiency with Microsoft products, the consulting team developed a custom workflow solution utilizing Microsoft SharePoint. This tailored remedy, instead of an entirely new software approach, yielded a durable solution the client that can easily implement and maintain in the future, without continuous and costly support requirements. The product also provides Mountain Home with a codified process for task assignments and information-sharing between multiple organizations such as project managers, contracting officers, comptrollers, and senior leadership.
As an added benefit, the workflow automatically produces and tracks key performance indicators to improve overall program efficacy and success.
Space Management
Another way the 366th Civil Engineer Squadron leveraged digital tools to transform processes is through ArcGIS Indoors, a technology that belongs to the Esri family of products, which the Air Force has an enterprise license for and is familiar with, in much the same manner as Microsoft products.
As a spatial analysis tool, ArcGIS Indoors can be used to optimize use of facility space. Utilization of facility space is contentious across the department. There are widely held beliefs that both the Air Force and Space Force have too many facilities; that the Department of the Air Force needs to optimize how facilities are used; and that installations are under-resourced (in staffing, skillset, and funding), which results in slow progress toward space utilization goals and incentives.
Due to manning limitations, it is common practice for bases to share space planning duties across real property officer, and engineer assistants. The tools used are typically primitive (Excel for space quantification and PowerPoint for visualization), and unfortunately, they drive narrowly focused, reactive planning instead of deliberate, holistic analysis.
Up to 10 hours per week were spent manually updating and maintaining a cumbersome project-tracking database, which the airmen described as “always out of date.” Clearly, an automated, digital solution was needed.
The 366th Civil Engineer Squadron was determined to find a better way of doing business through the utilization of ArcGIS Indoors. With some help, personnel collected occupancy data for over 50 different base facilities and applied space standards through the software to quickly and accurately show areas that are under-utilized and ripe for optimization. Additionally, the consultant team helped to integrate space requests and scenario planning, streamlining collaboration between agencies, boosting stakeholder transparency, and driving more effective strategic communication to save time and money.
This, however, only represents the tip of the iceberg for deployment of ArcGIS Indoors. There are multiple unexploited use-cases to explore, such as sensors that track electronic devices (with obvious applications in emergency response) and expediting facility work order execution through geo-location features.
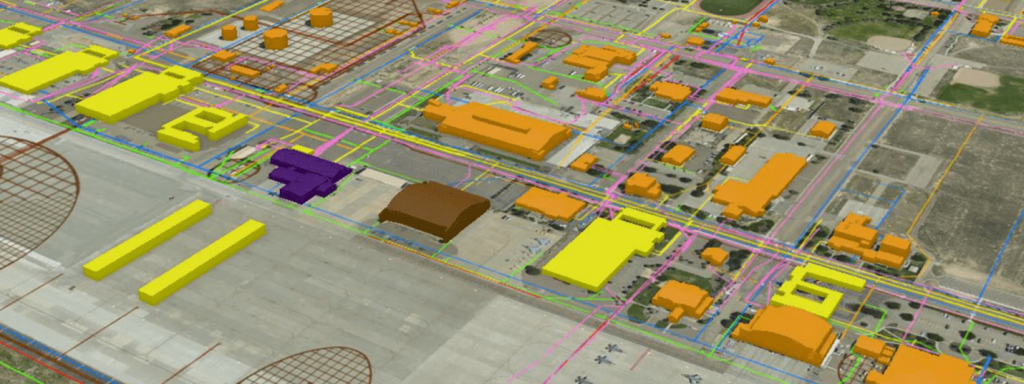
Developing a Digital Twin
A third way in which the 366th Civil Engineer Squadron is innovating is through deployment of a digital twin to support construction phasing. Beddown of the Qatar Emiri Air Force at Mountain Home will include hundreds of millions of dollars in construction through the remainder of the decade. The Republic of Singapore is looking at expanding its footprint as well through construction work, including a robust sustainment and repair program. The logistics underpinning these massive efforts has the base concerned about issues such as infrastructure capacity, equipment haul routes, and construction laydown areas. In response, JJR Solutions and Matrix Design Group developed a digital twin to visualize time-phased construction of installation projects that show potential problem areas, helping avoid the traditional, labor-intensive review of hard copy site plans laid on a conference room table or desk.
The transition from analog drawings to a digital twin mitigates the risk of errors and conflicts inherent in old methods, which are impossible to deconflict in an environment lacking in real-time visualization options.
Mountain Home further leveraged the data already available in Esri ArcGIS in the development of the digital twin. As a result, the installation is now able to quickly identify when new facilities will be built and when supply routes or laydown areas will be stressed as a result of competing projects. Armed with this information, the 366th Civil Engineer Squadron can work closely with all parties to mitigate issues before they happen, ensuring projects remain on schedule.
A Digital Toolbox
Mountain Home AFB believes that key components of these digital applications could be scaled up to provide enterprise-wide solutions. None of what has been developed is overly complex; rather, they are simple digital solutions founded in systems architecture that take advantage of considerable amounts of existing data on software already available.
The base civil engineer digital toolbox streamlines business processes and returns to personnel their most precious resource: time. This enables them to focus on increasing workloads and critical mission priorities. Mountain Home has leveraged this digital transformation to increase obligation rates by nearly 60 percent, despite an increased workload from two mission beddowns and current construction in excess of $500 million.
The technology and similar digital solutions are available to any Air Force installation: it just takes forward-thinking leaders to adopt it, and then accelerate change.
Zakary Payne, P.E., M.SAME, is Director, Government Consulting Services, Matrix Design Group; zakary.payne@matrixdesigngroup.com.
Tracy Meeks, P.E., M.SAME, is Engineering Flight Chief, 366th Civil Engineer Squadron, Mountain Home AFB, Idaho; maria.meeks@us.af.mil.
Lt. Col. Josh Aldred, Ph.D., P.E., PMP, M.SAME, USAF, is Assistant Professor, Department of Civil & Environmental Engineering, U.S. Air Force Academy, Colo.; josh.aldred@ afacademy.af.edu.
The views expressed are those of the authors and do not necessarily reflect those of the U.S. Air Force Academy, the U.S. Air Force, the Department of Defense, or the U.S. Government.
More News from TME
-
Developing a Space Planning and Optimization Program
Facility space planning and optimization program for a federal agency encourages close integration between contractors and stakeholders to ensure a properly informed and defined outcome. -
Quantifying Risk Through Probabilistic Risk Assessments
Research conducted at the Air Force Institute of Technology tested the feasibility of using existing facility condition and work task data to quantify the risk of mission failure due to infrastructure limitations and subsequently use the assessment to inform future funding decisions. -
Targeting Electric Grid Investments With Component-Level Modeling
An analysis of the Florida Panhandle electric grid conducted by the Air Force Institute of Technology identified vulnerable locations and opportunities for hardening targeted assets to optimize return on investment for resilience.